原料加工(原料抽出・精製)Material extraction / purification
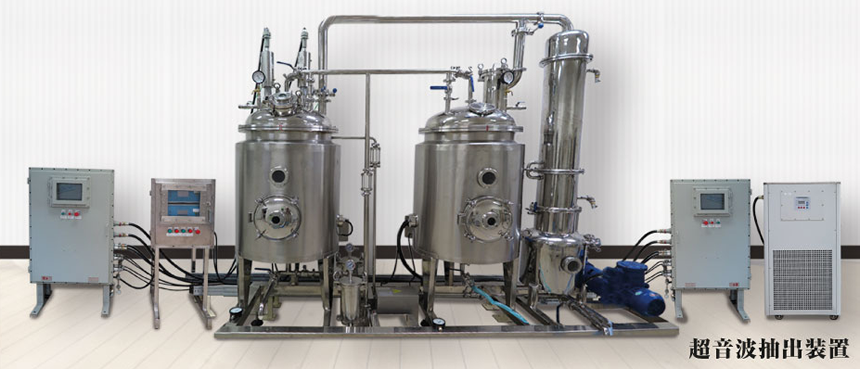
良いエキスを製造するには、目的や原料の特性に合わせることが大切です。
そして、各工程において最適な条件を選択し、様々な技術を組み合わせて、
目的物に最適な条件で製造することが肝心です。
エキス粉末は一般に以下に示した製造フローにより製造されます。
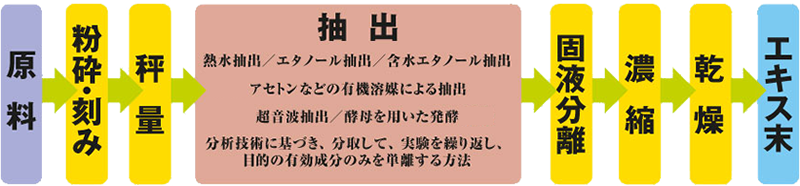
粉砕・刻み
原料に合わせた粉砕機を用いて、抽出に最適な大きさに粉砕します。
【1】ハンマーミル
ハンマーの付いたローターが高速回転しているところに原料が投入され、衝突による衝撃を繰り返し粉砕されます。粉砕された原料はスクリーンを通過して選択した粒度の原料が得られます。ハンマーの回転速度、スクリーンのサイズを変えることにより数百μmまでの粉砕が可能です。
【2】フェザーミル
粉砕機の構造はハンマーミルに類似していますが、ハンマーのかわりに鋭利な羽がついており、高速回転することにより、原料を剪断し、衝撃を繰り返し粉砕します。硬い原料などを粗粉砕する場合によく用いられる方法です。
【3】ピンミル
本体とドアのディスクに同心円状に取り付けられたピンが高速回転しているところに原料が投入され、衝突による衝撃を繰り返し粉砕されます。原料はビンが高速回転することによって起こる空気の流れにより分散、粉砕されていき粒度の細かくなったものからスクリーンを通り回収されます。回転速度、スクリーンのサイズを変えることにより数十μmまでの粉砕が可能です。スクリーンのないタイプの機種もあります。
【4】ジェットミル
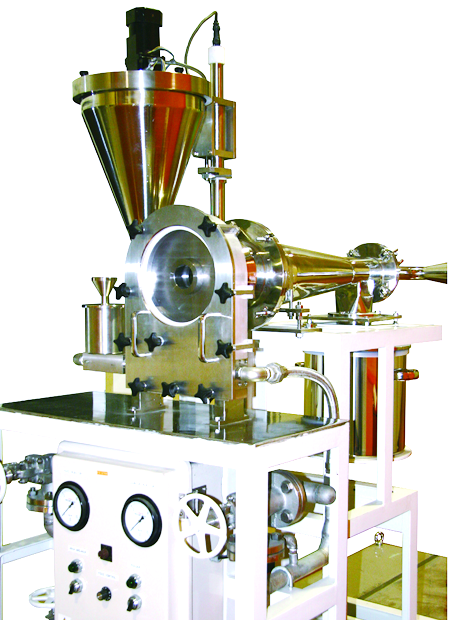
空気を圧縮し、ノズルの先端から噴出することにより高速の気流を起こし、その中で原料同士を衝突させ粉砕します。
他の衝撃原理の粉砕機で粉砕不可能な原料も粉砕することが可能であり、数μmまで細かくすることができます。
設備が高価で、コンプレッサーなど周辺機器も必要なためコストのかかる粉砕方法ですが健康食品原料などでよく用いられ、付加価値の高い原料の製造に適しています。
【5】AMCパルメライザー
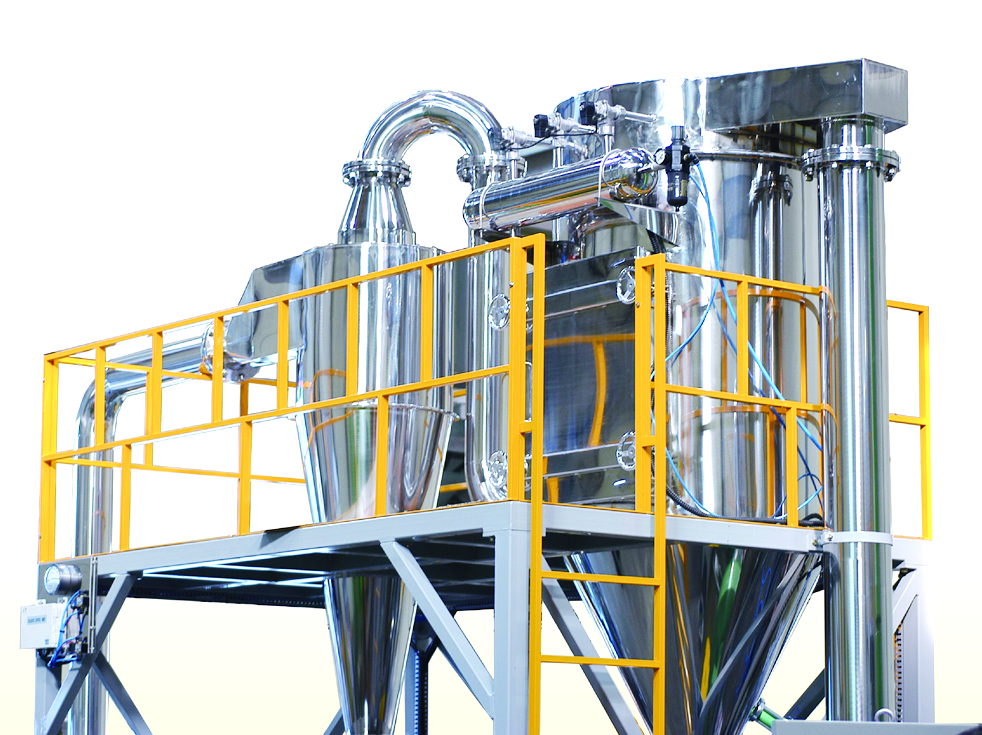
供給口から機内に送り込まれた原料は、粉砕ローターで効率的に粉砕されます。 その後、循環気流に乗って分級部へ送られた原料あるいは粉砕物は、分級作用を受け、微粉は分級ローター内側へ吸引されて製品として排出されます。また、遠心力を受けやすい粗い粒子は、カイドリング内側を通って粉砕部へ戻り、ハンマーとライナによる強い衝撃作用で再粉砕されます。
秤量
必要な原料を計量して、抽出釜に投入いたします。
抽出
【1】一般的な方法:熱水抽出/エタノール抽出/含水エタノール抽出
一般的には、熱水で抽出いたします。
目的成分によっては、エタノールや含水エタノールを用いることがあります。使用する熱水の量、温度、撹拌方法や時間、抽出時間など各種条件の決定にノウハウが必要です。
【2】特殊な抽出:アセトンなどの有機溶媒による抽出
原料素材から、油脂などの成分を効率よく抽出・採取するために使用されます。 植物油の抽出やガラナ成分の抽出に使用するアセトンなどがあります。これらの抽出溶剤は、最終食品の完成前に除去されなければなりません。
【3】技術を要する抽出:超音波抽出/酵母を用いた発酵
撹拌の代わりに超音波を用いて、細胞膜内レベルからの抽出を行う方法や、発酵により、酵母が持っている特定の物質のみを分解するという特徴を生かした、有効成分を壊さずに高品質なエキスを抽出方法も可能です。
【4】高度な化学技術を要する抽出精製:分析技術に基づき、分取して、実験を繰り返し、目的の有効成分のみを単離する方法
抽出されたエキスを更に生成することも可能です。液液分配や樹脂精製の他、分取クロマト技術を活かした高度な精製を行い、目的の有効成分のみを取り出すことも可能です。
固液分離
遠心分離やろ過などを行い、残渣と抽出液を分離します。
抽出物の性状により分離方法が異なります。
【1】遠心分離
一般的には、熱水で抽出たします。
遠心力を利用して、密度の異なる2種の液体、または液体と固体などの混合物を分離します。
【2】遠心ろ過
遠心力を利用して、ろ過を行い、液体と固体などの混合物を分離します。
【3】フィルタープレス
金属や樹脂製の凹凸のある中心に穴のあいたろ板にろ布を張ったものを直列に密着させたもので、抽出液をポンプでろ板中心の穴から加圧圧入します。その圧力で、抽出液のみが2枚のろ板の隙間のろ布の日から外へ排出されます。
濃縮
抽出液の水分を減圧下で飛ばしていきます。
抽出物の特性により温度条件等が異なります。
乾燥
必要に応じて、乾燥を行います。目的成分の特性やエキスの性状により異なりますが、出来るだけ低温で短時間に乾燥することが望まれます。乾燥方法は、次の中から選択可能です。
【1】真空乾燥機
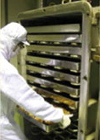
大気圧以下の減圧下(真空)では、水の沸点が下がり、比較的低温で水が蒸発することを利用した乾燥方法で、常圧で行う熱風乾燥に比べて短期間での乾燥が可能となり、色などの変化も小さいです。これも日常的に行われている乾燥方法で原体原料から粉末、顆粒まで幅広く使用されます。
【2】凍結乾燥機(フリーズドライ)
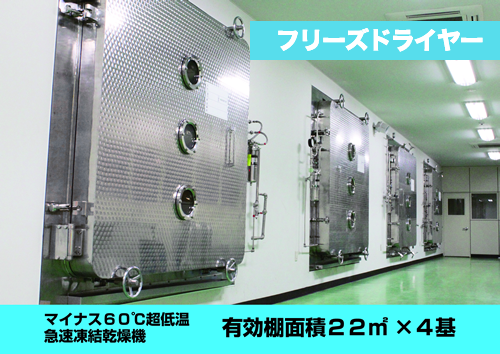
凍結状態にある原料から減圧により氷を昇華させて水分を除去します
【3】熱風循環棚式乾燥機
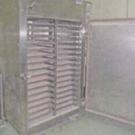
棚式で熱風が庫内を循環する乾燥機です。浅いトレーに原料をのせて棚に入れていきます。原体原料から粉体の乾燥まで幅広く利用されています。汎用性が高いですが、原料によっては乾燥時間が長くなってしまうものもあり、効率を配慮する必要があります。乾燥による変色の程度も比較的厳しいので、色や香りを気にしない原料によく用いられます。
【4】流動層乾燥機
底面から送り込まれる熱風により粉末を流動させ、短時間に乾燥させます。従って原料は流動できるものでなくてはいけません。原料を熱風により流動させるメリットは次のとおり。
- 流動しながら粉末原料と熱風がよく混ざり合い、接触面積が大きくなるので効率の良い乾燥が行える。従って装置容量に対して処理量が大きい
- 分散状態で乾燥されるので表面部分と内部における乾燥の差が小さくなる。言い換えると限界含水率が小さくなるので、製品温度は低く保たれ、乾燥時間が短くなる。粉体原料の乾燥から造粒品の乾燥などによく使用される。
【5】噴霧乾燥機(スプレードライ)
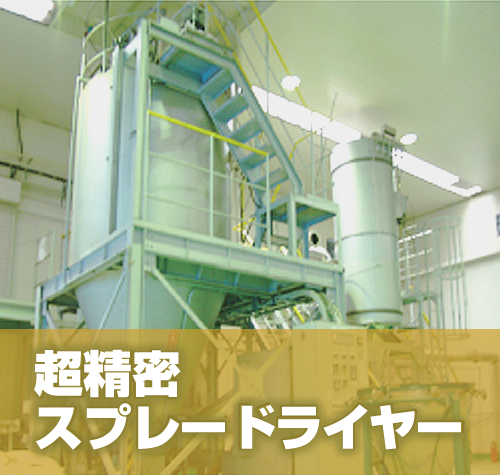
噴霧乾燥機は容量の大きな乾燥室内に液状原料を霧状に噴霧して熱風と接触させて乾燥します。従って仕上がり品は60~200μmの微粉末状になります。主にエキス抽出後に噴霧乾燥してエキス末とすることが多いです。噴霧状態により仕上がりの粒度などが変わりますが、噴霧には回転板、加圧ノズル、二流体ノズルがよく用いられています。乾燥室内には120~200℃程度の熱風が送り込まれまます。
【6】その他
マイクロウェーブ乾燥など。
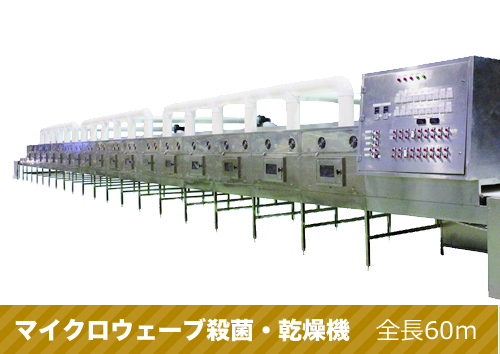
完成したエキス末
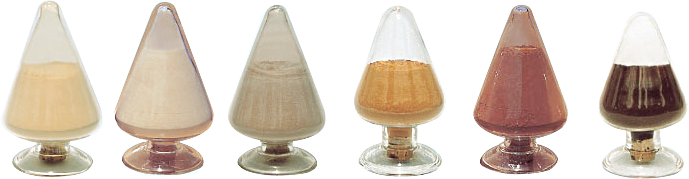